企业的设备指标对生产和运营有重要的指导意义,涵盖多个方面,用于评估设备的性能、可靠性、维护状况和整体运营,对运营效率提升、生产计划优化、成本控制、提高设备寿命等都有直接作用。
本文主要介绍设备维护管理指标中的故障率和完好率,主要用于评估设备维护状况和效率,与设备整体性能和可靠性相关。

1、故障率
设备在一段时间内发生故障的频率,表示设备的可靠性。

数值越高,表示设备容易发生故障,可靠性较低。反之则表示设备在一段时间内发生故障的频率较低,具有较高的可靠性。
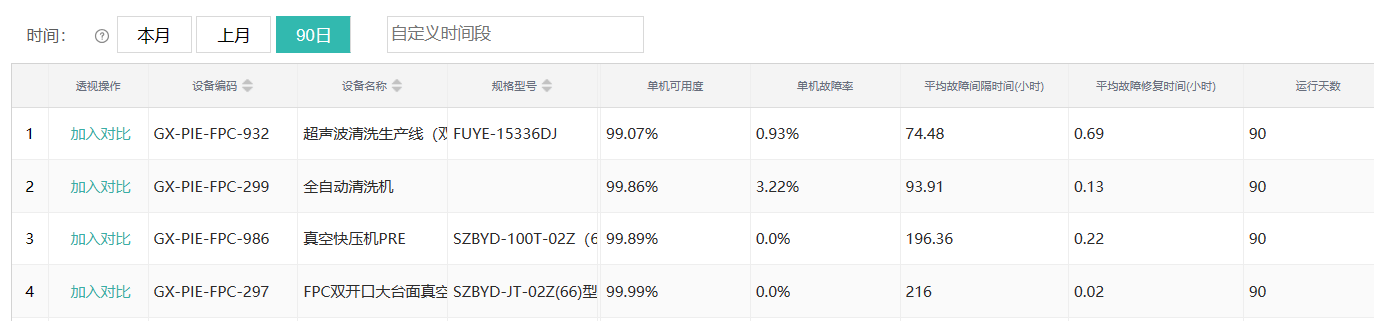
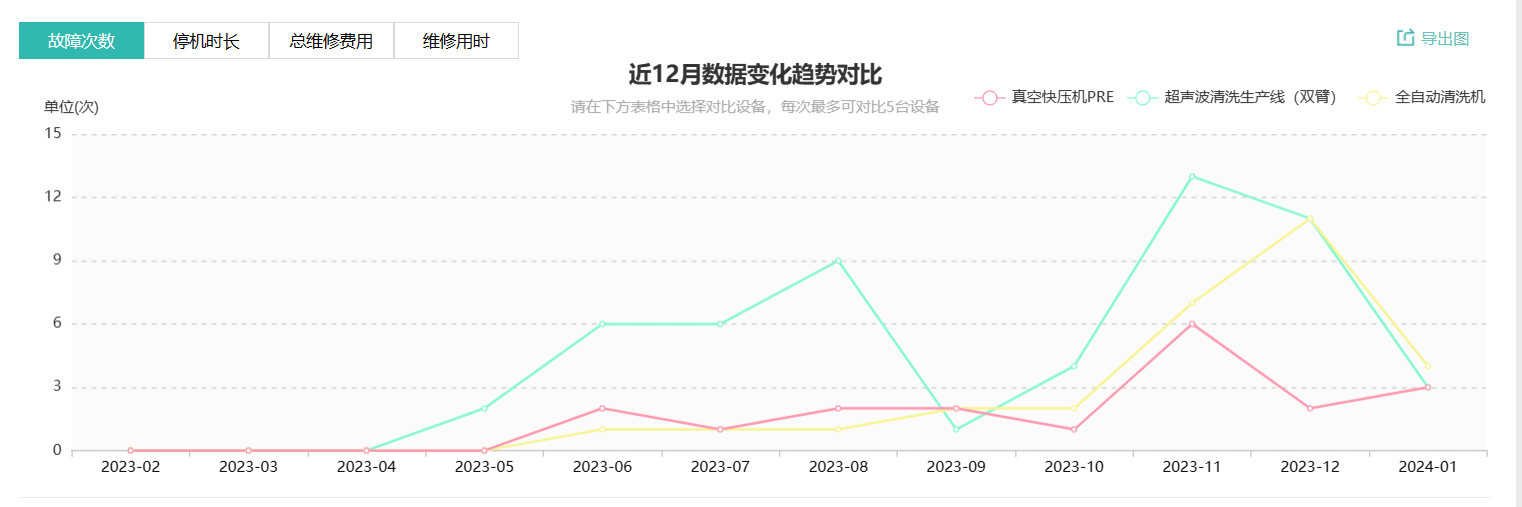
2、完好率
设备在一段时间内正常运行的时间占总时间的比例,反映设备的可用性。

数值越高,表示设备在大部分时间内都能正常运行,具有较高的可用性和稳定性。反之则代表设备存在较多的故障和停机,可用性较低。

完好率通常与故障率相互补充。完好率高意味着故障率相对较低,设备更加可靠。反之亦然,高故障率可能导致完好率下降。

指标能直接反馈运营生产中存在的问题,对于发现的问题,我们可以按照以下方法进行问题解决。
(1)制定维护策略
(2)优化生产计划
(3)采用预防性维护
(4)绩效评估和持续改进
例如:
一家制造企业拥有自动化生产线,生产关键零件。通过分析完好率和故障率数据,发现完好率为90%,故障率为10%。企业需要分析具体原因,并制定新的维护策略。
第一步:分析故障停机原因
对这台机器的故障停机原因进行深入分析。了解是哪些故障或问题导致了停机,包括设备故障、维护周期安排、零部件更换等。
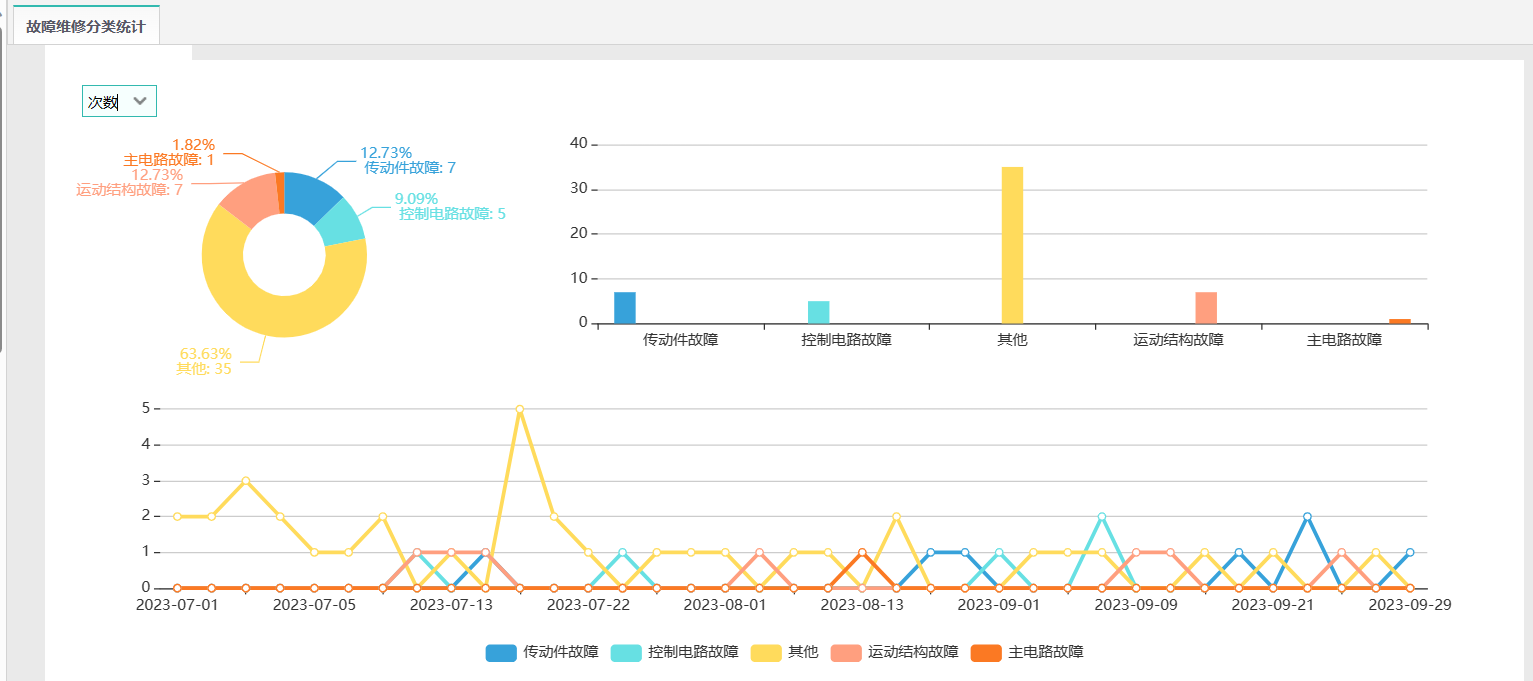
第二步:制定维护策略
增加预防性维护的频率,特别是对那些容易故障的零部件进行重点关注,以防止意外停机。包括定期检查、润滑、清洁和零部件更换。确保维护工作易于执行,可以尽量减少故障时间。
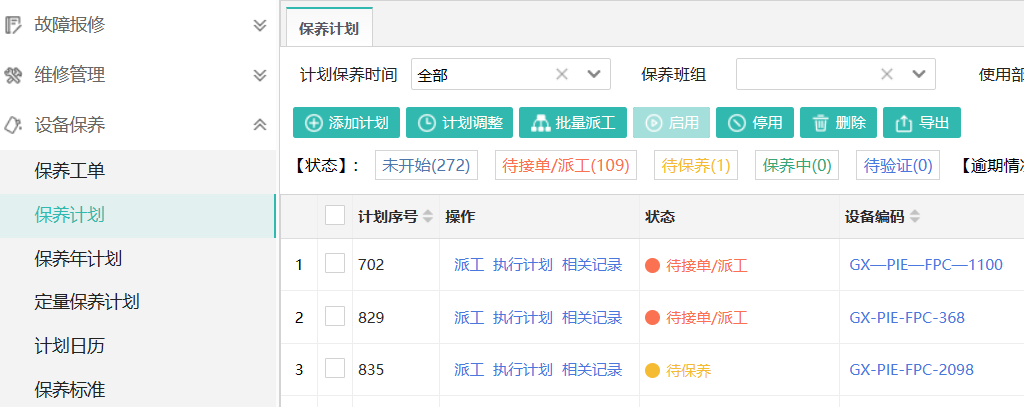
第三步:优化生产计划
企业在考虑可用度和运行时长的基础上,结合维护数据反馈,通过设立实时监测系统,定期评估运行时长,基于实际运行数据将维护计划纳入生产计划调整,确保维护工作与生产计划协调。
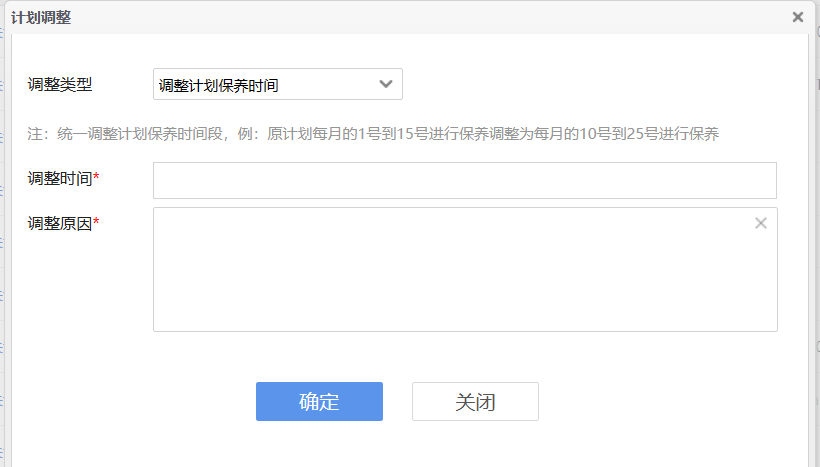
第四步:绩效评估和持续改进
设定完好率、故障率的具体指标,定期进行绩效评估,识别改进空间,在一到四步之间不断循环,最终促使企业优化了设备管理工作,还在持续改进中实现了生产效率的提升,降低了维护成本。
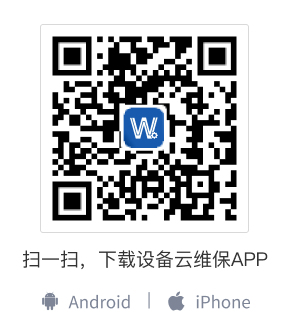